Износостойкая (или износостойкая) литая сталь относится к литой стали с хорошей износостойкостью.По химическому составу она подразделяется на нелегированную, низколегированную и легированную износостойкую литейную сталь.Существует множество типов износостойких сталей, которые можно условно разделить на высокомарганцевую сталь, средне- и низколегированную износостойкую сталь, хромомолибденово-кремниево-марганцевую сталь, кавитационно-стойкую сталь, износостойкую сталь, и специальной износостойкой стали.Некоторые легированные стали общего назначения, такие как нержавеющая сталь, подшипниковая сталь, легированная инструментальная сталь и легированная конструкционная сталь, также используются в качестве износостойкой стали при определенных условиях.
Средне- и низколегированные износостойкие стали обычно содержат такие химические элементы, как кремний, марганец, хром, молибден, ванадий, вольфрам, никель, титан, бор, медь, редкоземельные элементы и др. Вкладыши многих крупных и средних шаровых мельницы в США изготавливаются из хромомолибдено-кремнемарганцевой или хромомолибденовой стали.Большинство мелющих шаров в США изготовлены из средне- и высокоуглеродистой хромомолибденовой стали.Для заготовок, которые работают при относительно высоких температурах (например, 200~500 ℃) в условиях абразивного износа или поверхности которых подвергаются относительно высоким температурам из-за теплоты трения, сплавы, такие как хромомолибденванадий, хромомолибденванадийникель или хромомолибденванадийвольфрам может быть использован.
Истирание – это явление, при котором материал на рабочей поверхности объекта непрерывно разрушается или теряется при относительном движении.По механизму износа износ можно разделить на абразивный износ, адгезионный износ, коррозионный износ, эрозионный износ, контактно-усталостный износ, ударный износ, фреттинг-износ и другие категории.В промышленной сфере абразивный износ и адгезионный износ составляют наибольшую долю отказов деталей из-за износа, а виды износа, такие как эрозия, коррозия, усталость и истирание, имеют тенденцию возникать при работе некоторых важных компонентов, поэтому они становятся все более распространенными. и больше внимания.В условиях эксплуатации часто одновременно или последовательно возникают несколько форм изнашивания, а взаимодействие изнашивания принимает более сложный вид.Определение типа износа изделия является основой для разумного выбора или разработки износостойкой стали.
Кроме того, износ деталей и узлов является проблемой системотехники.Существует множество факторов, влияющих на износ, в том числе условия работы (нагрузка, скорость, режим движения), условия смазки, факторы окружающей среды (влажность, температура, окружающая среда и т. д.), материальные факторы (состав, организация, механические свойства), поверхность качество и физико-химические свойства деталей.Изменения каждого из этих факторов могут изменить степень износа и даже изменить механизм износа.Видно, что материальный фактор является лишь одним из факторов, влияющих на износ заготовки.Чтобы повысить износостойкость стальных деталей, необходимо начать с общей системы трения и износа в конкретных условиях для достижения желаемого эффекта.
1. Термическая обработка на раствор (водоупрочнение) отливок из износостойкой высокомарганцовистой стали.
В литой структуре износостойкой высокомарганцовистой стали имеется большое количество выделенных карбидов.Эти карбиды снижают ударную вязкость отливки и облегчают ее разрушение во время использования.Основная цель термической обработки на твердый раствор отливок из высокомарганцовистой стали состоит в том, чтобы удалить карбиды в литой структуре и на границах зерен для получения однофазной аустенитной структуры.Это может улучшить прочность и ударную вязкость стали с высоким содержанием марганца, так что отливки из стали с высоким содержанием марганца подходят для более широкого круга областей.
Термообработку на твердый раствор отливок из износостойких высокомарганцовистых сталей можно условно разделить на несколько этапов: нагрев отливок до температуры выше 1040°С и выдержка их в течение соответствующего времени для полного растворения содержащихся в них карбидов в однофазном аустените. ;затем быстро охлаждая, получают структуру твердого раствора аустенита.Эта обработка раствором также называется обработкой для повышения жесткости воды.
(1) Температура закалки водой
Температура водостойкости зависит от химического состава стали с высоким содержанием марганца, обычно от 1050 ℃ до 1100 ℃.Высокомарганцевые стали с высоким содержанием углерода или высоким содержанием легирующих элементов (такие как сталь ZG120Mn13Cr2 и сталь ZG120Mn17) должны соответствовать верхнему пределу температуры водостойкости.Однако чрезмерно высокая температура водостойкости вызовет сильное обезуглероживание поверхности отливки и быстрый рост зерен стали с высоким содержанием марганца, что повлияет на характеристики стали с высоким содержанием марганца.
(2) Скорость нагрева при закалке водой
Теплопроводность марганцевой стали хуже, чем у обычной углеродистой стали.Отливки из высокомарганцовистой стали имеют высокие напряжения и легко трескаются при нагреве, поэтому скорость нагрева следует определять в зависимости от толщины стенки и формы отливки.Вообще говоря, отливки с меньшей толщиной стенки и простой конструкцией могут нагреваться быстрее;отливки с большей толщиной стенки и сложной структурой должны нагреваться медленно.В процессе фактической термообработки, чтобы уменьшить деформацию или растрескивание отливки во время процесса нагрева, ее обычно нагревают примерно до 650 ℃, чтобы уменьшить разницу температур внутри и снаружи отливки, а температуру в печь однородна, а затем быстро поднимается до температуры вязкости воды.
(3) Время выдержки при обработке водой для повышения жесткости
Время выдержки гидрозакалки в основном зависит от толщины стенки отливки, чтобы обеспечить полное растворение карбидов в литой структуре и гомогенизацию аустенитной структуры.В нормальных условиях его можно рассчитать, увеличивая время выдержки на 1 час на каждые 25 мм увеличения толщины стенки.
(4) Охлаждение при закалке водой
Процесс охлаждения оказывает большое влияние на индекс производительности и структуру отливки.Во время гидрозакалки температура отливки перед входом в воду должна быть выше 950°C, чтобы предотвратить повторное осаждение карбидов.По этой причине временной интервал между выливкой из печи и входом в воду не должен превышать 30 секунд.Температура воды должна быть ниже 30°C перед попаданием отливки в воду, а максимальная температура воды после входа в воду не должна превышать 50°C.
(5) Твердый сплав после гидрозакалки
После гидрозакалки, если карбиды в стали с высоким содержанием марганца полностью удалены, металлографическая структура, полученная в это время, представляет собой единую аустенитную структуру.Но такую структуру можно получить только в тонкостенных отливках.Обычно допускается небольшое количество карбидов в аустенитных зернах или на границах зерен.Нерастворенные карбиды и осажденные карбиды могут быть снова удалены путем термической обработки.Однако эвтектические карбиды, выделенные из-за чрезмерной температуры нагрева во время гидрозакалки, неприемлемы.Потому что эвтектический карбид не может быть снова удален термической обработкой.
2. Дисперсионно-упрочняющая термическая обработка отливок из износостойкой стали с высоким содержанием ганганца.
Дисперсионно-упрочняющая термическая обработка износостойкой высокомарганцовистой стали относится к добавлению определенного количества карбидообразующих элементов (таких как молибден, вольфрам, ванадий, титан, ниобий и хром) посредством термической обработки для получения определенного количества и размера в высокомарганцевая сталь Вторая фаза дисперсных карбидных частиц.Эта термообработка может укрепить аустенитную матрицу и повысить износостойкость стали с высоким содержанием марганца.
3. Термическая обработка отливок из износостойкой среднехромистой стали.
Целью термической обработки отливок из износостойкой среднехромистой стали является получение мартенситной матричной структуры с высокой прочностью, ударной вязкостью и высокой твердостью для повышения прочности, ударной вязкости и износостойкости стальных отливок.
Износостойкая среднехромистая сталь содержит больше элементов хрома и обладает более высокой прокаливаемостью.Поэтому его обычный метод термообработки: после 950 ℃-1000 ℃, его аустенизация, затем закалка и своевременный отпуск (обычно при 200-300 ℃).
4. Термическая обработка износостойких отливок из низколегированных сталей.
Износостойкие отливки из низколегированных сталей обрабатывают закалкой в воде, закалкой в масле и закалкой на воздухе в зависимости от состава сплава и содержания углерода.Перлитная износостойкая литая сталь проходит термообработку нормализацию + отпуск.
Для получения мартенситной матрицы с высокой прочностью, ударной вязкостью и твердостью, а также для повышения износостойкости стальных отливок отливки из износостойких низколегированных сталей обычно подвергают закалке при 850-950°С и отпуску при 200-300°С. .
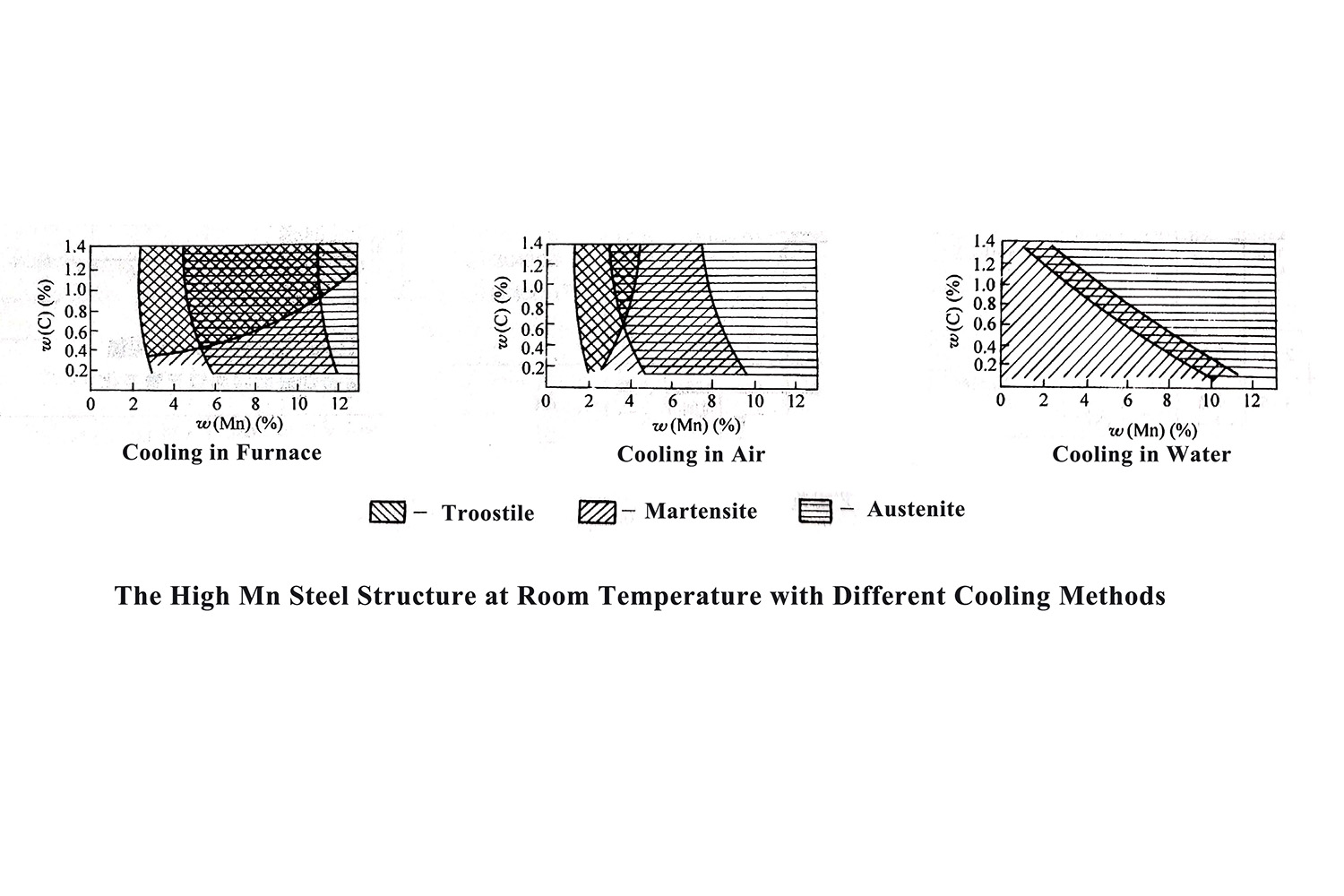
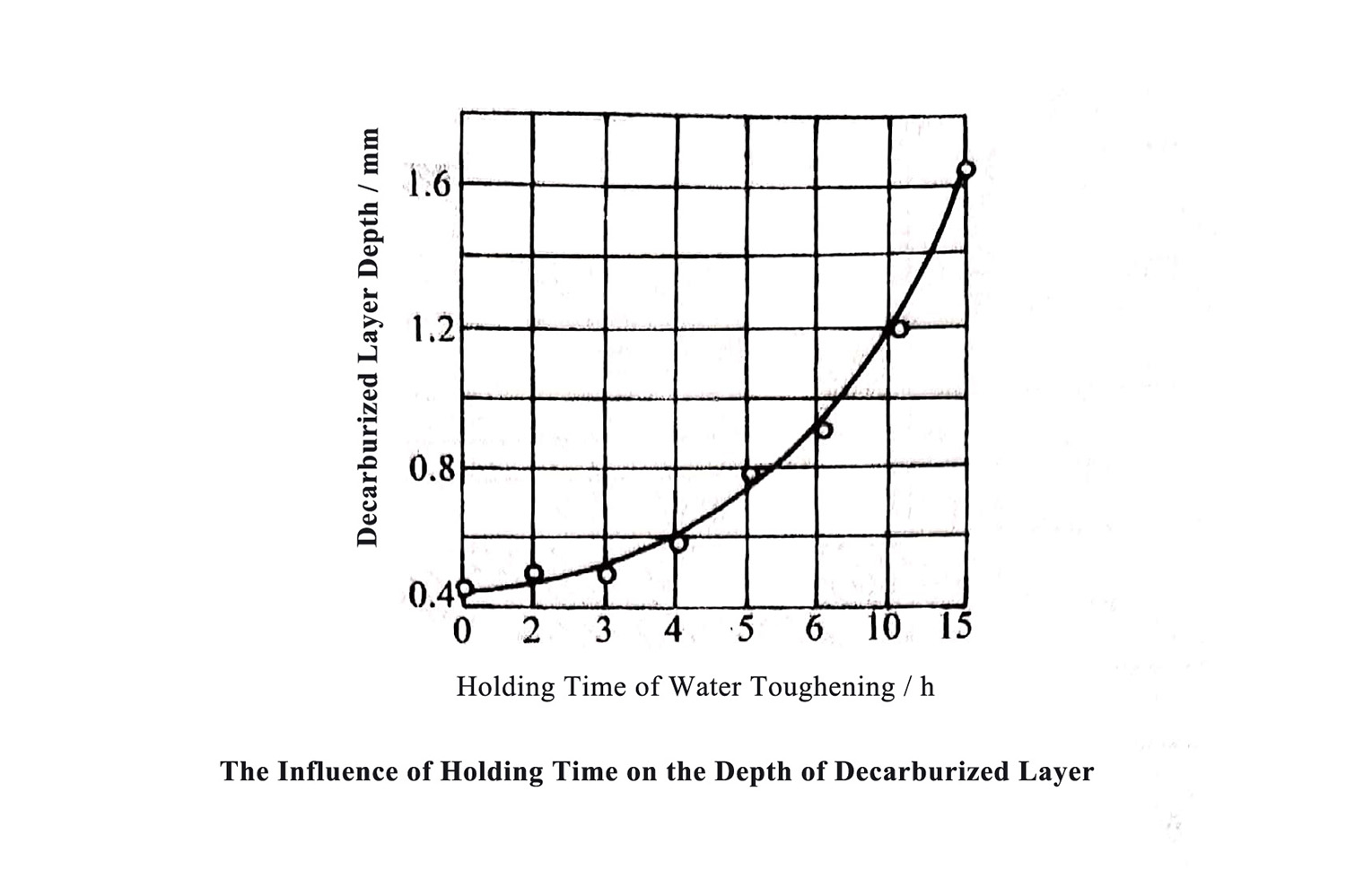
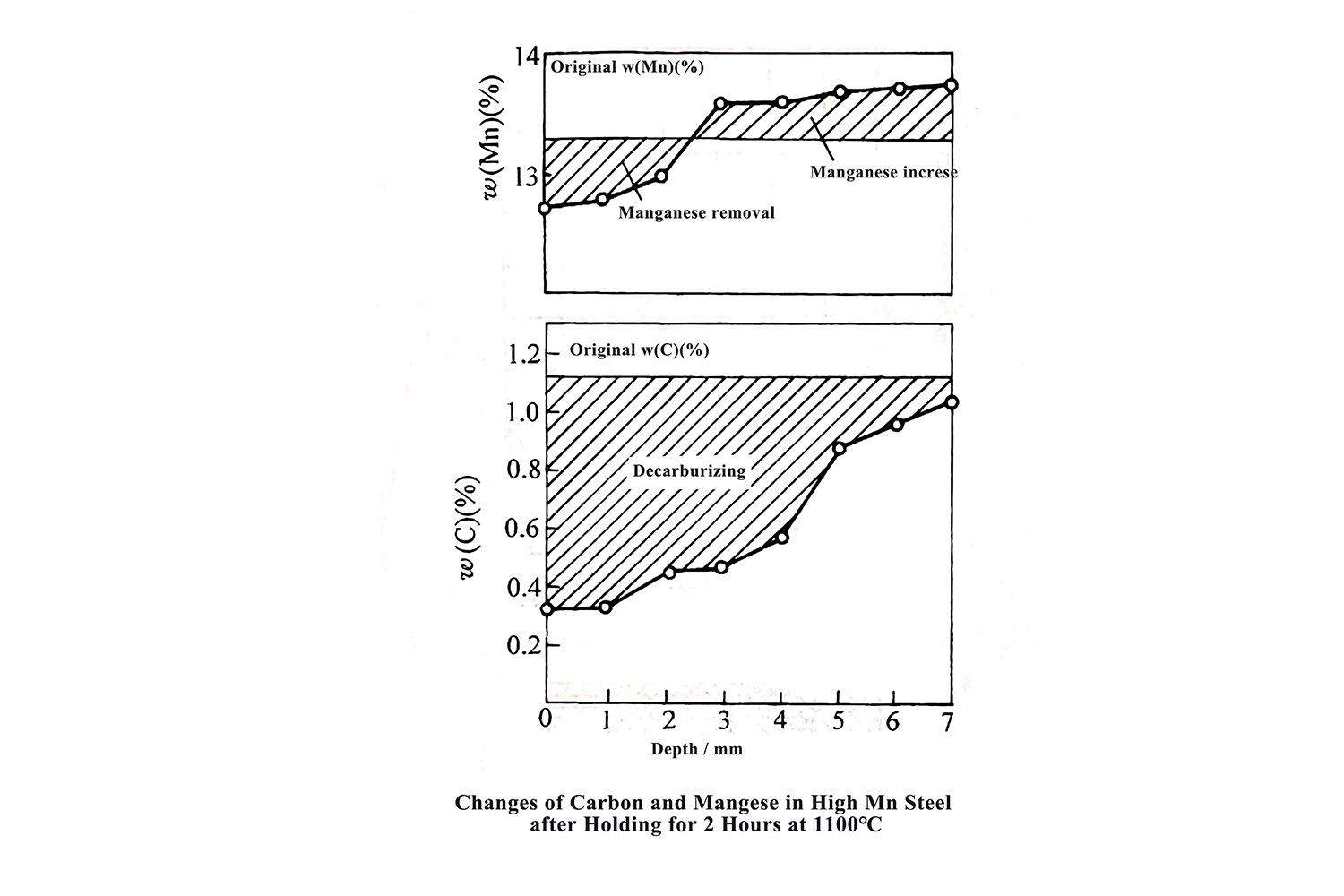
Время публикации: 07 августа 2021 г.